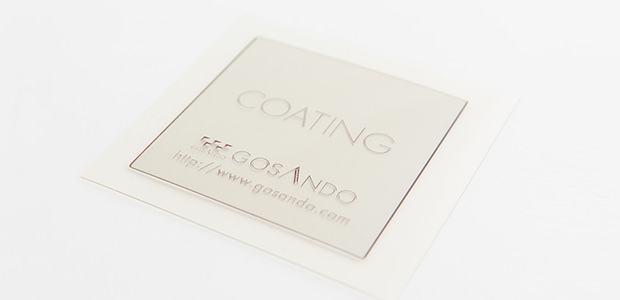
Advantages of using flexo plates for varnish coating
- Flexo varnish coating plates are compatible with a variety of coating agents such as water-based and UV varnishes.
- Compared to other methods, flexo plates have excellent printing resistance and with recent mechanical improvements, register accuracy has been greatly improved.
- Even with just a spot coat, if there is a spot you want to especially stand-out, it can be done with high precision.
- In order to apply the large amount of varnish needed for a glossy finish it is critical that the plate surface is smooth and precise. Flexo plates with their high smoothness are exceptionally suited for this application.
- Varnish coat plates are often used to apply an underprint for pearl, gold, silver, etc. Flexo plates can produce this unique luster while also remaining environmentally friendly. A huge place in today’s modern nature conscious society.
- Beyond contact printing, flexo varnish coating can be used for many other applications as well
Watanabe Gosando boasts one of the largest shipments of coating plates in Japan. We have the technology and experience to keep pace with this ever-evolving industry in order to meet our customers’ standards.
Our flexo varnish plates are able to maintain even the strictest register accuracy. Please feel free to contact us if you need flexo based varnish coating plates with exceptional accuracy.
Varnish plate technology
About varnish plate materials: For varnish coatings – and pearl/silver undercoatings – it is very important to select a compatible resin material. Currently, Asahi Kasei is a major domestic producer, though foreign manufacturers such as DuPont, XSYS also provide resin specialized for this application.
What is the best resin for varnish coating?
There are many resin materials dedicated to varnish plates, however the most important question is how the varnish will interact with the plate material. If they are compatible then the varnish can be applied to the plate with no problems. However, if the materials have an adverse reaction, then the surface of the plate will swell causing uneven printing.
The varnish plate registration marks don’t match!?
The varnish plate is formed by changing the magnification of the surface formation according to the thickness and traits of the resin plate, and the specifications of the printing machine. If at that time the magnification value is different, then the registration marks won’t match. Of course, misalignment can occur due to changes in the paper as well, however it is important to check the plate for accuracy as well.
How can I ensure a clean-looking varnish coat?
The first step is to choose the correct resin plate. If the resin plate and coating ink are not compatible then it will be almost impossible to get a clean varnish effect. Smooth and even printing is more important for coating than applying a lot of ink.
What factors cause haloing to appear on varnish?
People tend to assume printing pressure is the main cause, however it is often caused by factors such as anilox pressure, uneven molding of the resin plate, or incompatibility between the resin plate and the coating ink.
Is it possible to have a coating design with strict registration marks?
Currently designs utilizing varnish coating are becoming a global trend. It is also used in many fields to create expressive designs, lettering, or images. In recent years, the accuracy and materials of resin plates has been steadily improving which opens up a wealth of applications.
How does a resin plate become uneven?
Unevenness will occur depending on the platemaking method and materials. The most common problem after platemaking is unevenness caused by insufficient aging. After the resin plate is made, as a general rule, it must be left to sit for about 24 hours to allow all of the solvent used during its production to escape the material. If a plate is delivered to a printing facility and used immediately, then it may become uneven. In this case however, the solvent in the resin plate will disappear over time causing the surface to smooth. If the plate material and coating ink are not compatible then the plate can swell, causing unevenness. This is because both the coating ink and plate material are chemically reactive substances, which can lead to the ink permeating the surface of the plate. To avoid this please choose an ink which suits your plate or use a plate which is compatible with your preferred ink.
What is back-trapping!?
Problems may occur when the resin plate accidentally spreads partially dried ink. First, check the drying of the printing ink and the compatibility of the varnish. If the problem doesn’t go away after that then it may be necessary to change the plate type. There are various types of resin plates compatible with varnish and back-trapping can sometimes be eliminated by changing styles.
What do I do if I want to apply more varnish?
When trying to increase the coating amount it can be highly effective to replace the anilox roll with one that has larger cell volumes. However, since this involves replacing a part of the press itself this process can be quite the ordeal. In order to increase the supply with just the resin plate you can choose a material with a higher transferability or through certain processing methods.
What are the differences between a resin plate and cut plate?
Typically, resin plates are made by irradiating a material called photosensitive resin with light. Cut plates are made by cutting synthetic rubber or blankets with a cutting plotter. Resin plates have high accuracy and durability, however cutting plates often have cost advantages.
If you have any questions about varnish plates, please use the contact form below.
Contact us