What is flexographic printing and platemaking?
The printing method taking the packaging world by storm
In recent years, flexographic printing, often referred to simply as “flexo”, has become a major trend in the United States and Europe. In fact, most packaging in the European market is now printed flexographically.
From gravure to flexographic printing
This shift from gravure printing to flexo printing has become evident in the flexible packaging industry. In Japan however, while the superiority of flexo printing from the perspectives of both productivity and environmental impact are acknowledged, however the movement to introduce and utilize flexo printing has not been nearly as enthusiastic as in Europe.
This is particularly true among applications and clients which emphasize print reproducibility above all else, where offset and gravure still maintain a slight advantage.
However, due to the progress of CTP flexo printing and the improvement of register accuracy with the advent of gearless printing machines, the quality of printing within Japan has advanced drastically in recent years.
On the equipment side, Japan is entering a period of demand for replacement presses, against the backdrop of active innovation, it is certain that the Japanese flexo market is primed for future growth.
Flexo opens the way for more printing possibilities
High reproducibility in all mediums
If you’re thinking “I want to differentiate my product with gorgeous colors and eye-catching packaging,” then flexo is for you. Not only does it exhibit a high print reproducibility but it also uniquely able to print on almost any surface regardless of roughness, elasticity, or changing thickness.
In flexographic printing, water-based or UV reactive ink is applied to a thick, highly elastic resin plate using an anilox roll, and printing is performed directly on the substrate’s surface.
For this reason, flexo can flexibly handle uneven paper, film, cloth, unwoven fabric, and more; on even elastic and materials of varying thickness, all while outputting 8 colors with a high degree of reproducibility.
Ideal for products demanding print quality
To continue, flexo also excels at extremely thin uniformity solid printing, and with the application of various resins and chemicals, it is possible to further improve accuracy.
Recently, advances in flexo printing equipment, materials, and production technology have made it possible to create sophisticated multicolor depictions with a high line count.
Not only can fine detail be reproduced consistently in high fidelity, the ability to gradate colors is also increased. For example, you express gradation of anywhere from 2-98% with 150 lines per centimeter.
Safety your whole family can trust
By passing the Pollution Release Transfers Register (PRTR) requirements, you can be sure it’s safe for food and pharmaceuticals
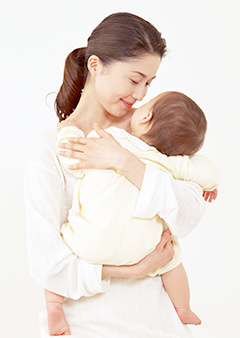
While flexo can use solvent inks it also works with a wide range of water-based and UV curable inks as well, and flexo specific inks have come to be regarded in the U.S. and Europe as some of the most environmentally friendly. This has helped expand its market share into direct-contact food and pharmaceutical packaging.
Flexo printing to protect people and the environment
It also requires less ink to get the same effect as other printing methods, it leaves behind less residual solvent making it safe for consumable products. Furthermore, since it uses alcohol-based solvents so it also meets the PRTR’s definition of environmentally safe.
High productivity achieved by flexo printing
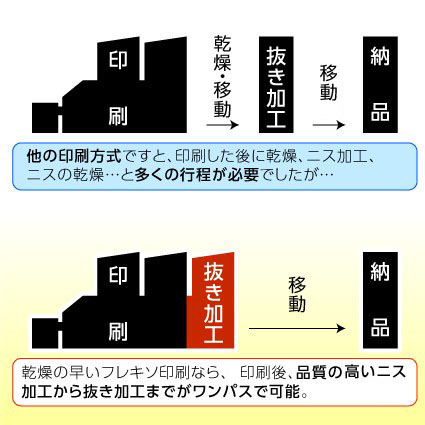
One of the advantages of flexo printing is high productivity.
Flexo presses can print directly from the roll along with die-cutting and processing all in one-pass, making printing faster than ever before. This added efficiency in going from start to finish without interruption makes flexo highly suitable for high-mix low-volume that’s been trending in recent years.
When looking at the whole of the printing process it’s easy to see how this strong affinity for inline processing provides high improvements to efficiency, productivity, and quality control which makes flexo a winning bet for the future.
Durable and long-lasting. Our extra resistant high-quality plates
Watanabe Gosando uses resins carefully selected according to various printing specifications.
Our flexographic resin plates are wear-resistant enough to print 1 million times, and achieve consistent, precise reproducibility even when printing large lots.
These resins are several times more resistant to printing than conventional materials and it could be said that they play an important role in supporting the packaging industry.
The characteristics of different printing methods:
Print Method | Flexo | Offset | Gravure | Screen | Inkjet |
---|---|---|---|---|---|
Plate Style | letterpress | lithography | intaglio | stencil | digital file |
Transcription Method | direct | indirect | direct | direct | direct |
Print Speed | fast | medium | fast | slow | slow |
Ink Type | various | oil-based | oil-based | various | limited |
Print Accuracy (Average) | ◎ | ◎ | ◎ | △ | ◯ |
Fine Line Accuracy | ◎ | ◎ | ◯ | △ | △ |
Ink Density | ◎ | ◯ | ◯ | ◎ | ◯ |
Print Media | various | mainly paper | paper/film | various | various |
Permitted Media Roughness | slightly rough | smooth | smooth | rough | rough |
Permitted Media Thickness | various | consistent thickness | consistent thickness | various | various |
Feed Method | mainly web-fed | mainly sheet-fed | web-fed | sheet-fed | sheet or web fed |
Press Cost | moderate | high | high | moderate | low |
Plate Cost | moderate | low | high | high | none |
Environmental Friendliness | ◎ | △ | △ | △ | △ |
Prevalence | △ | ◎ | ◎ | △ | ◯ |
Applications for flexographic plates
Printing
- Corrugated
- Paper Goods
- Drink Cartons
- Flexible Packaging Material
- Paper Bags
- Cloth Bags
- Envelopes
- Tissue Paper
- Paper Napkins
- Stickers
- Shrink Labels
- Anti-counterfeit Printing
- Foil
- Lumber
- Cloth
- Tape
- Sheet Steel
Coating
- Matte/Gloss
- Adhesive
- Anti-slip
- Insect Repellant
- Water Repellant
Embossing
- Paper Embossing
Molding
- Metal Casting