Decorative Cardboard / Process Printing
In Japan, most of the plates made for full-color corrugated process printing are made by our company. From post-printing (direct printing) to pre-printing, we have acquired a wealth of knowledge and achievements through the challenges posed to us by our customers, and emerged with the largest market share of corrugated flexo plates in Japan.
Making flexo plates for corrugated process printing (both pre- and post-print) goes beyond simply understanding color management.
We offer finely tuned flexo plates for corrugated application by considering all aspects of your print job, everything from compatibility of the ink and plate material to that of the machine and corrugated substrate.
Cardboard Pre-printing (Process Printing)
More than 90% of Japanese decorative cardboard packaging is pre-printed.
Pre-printing for corrugated manufacturing is performed separately on the front liner board before being glued together with a core and back liner to form a complete corrugated sheet.
Because this pre-printing happens before the corrugated sheet is assembled, the front liner maintains a flat surface which is easy to print on. After assembly however, the structure of the core leads to unevenness on the surface, making it harder to print.
Ink won’t stick correctly if proper pressure can’t be applied. Therefore, printing on corrugated sheet directly rather than pre-printing can result in haloing and loss of proper color control. Thus, by pre-printing on the smooth liner board you can ensure proper pressure for clean prints.
Alternatively, offset can be used to print onto a white liner paper and then laminated onto the surface of the corrugated sheet, however the inks typically used for this process are oil-based which are worse for the environment. This method also has the additional drawback of being more expensive.
That said, this method can be quite efficient for making eye-catching packages in smaller lot quantities and is often used for full color home appliance packaging.
On the other hand, pre-printing water-based ink which is environmentally friendly.
Printing directly onto single sheet liner board also advantages flexo over offset due to the former’s superior ink adhesion. It should be noted however, that printing direct to liner board is not efficient for smaller runs as it is processed on a rotary press.
This method is favored in Japan for large lot products such as major beer brands.
The current accuracy of pre-prints in Japan is 50 to 100 lines with a registration error of 0.5mm, which is a little rough compared to Europe and the U.S. (European and American pre-prints typically have 80 to 120 lines and a registration error of 0.3mm)
These differences are due to the differences in precision of the printing machines, substrate, and resin plate being used. Specifically, in Europe and America it is common to see resin plates with a thickness of 1.7 mm or less, while in Japan they are usually closer to 2.54 mm. Resin plates are noted for producing cleaner prints with thinner plates, however if the surface is not smooth then thin plates might not apply evenly to the substrate, leading to various errors such as color variation or feathering.
The level of quality control maintained in Japan is extremely high, so most major companies use pre-prints for their main products.
Cardboard Direct Process Printing (Post-printing)
Whereas pre-printing prints the image onto the liner board prior to corrugated production, post-printing prints the image directly onto the corrugated sheet.
The benefit of this is a reduction of overall waste and the ability to print smaller lots, at the expense of a slight reduction in print accuracy.
Current Japanese post-processing has 45 to 70 lines of accuracy, rougher than pre-print’s 50 to 100 lines, and considerably rougher than offset’s standard of 175 lines.
In Europe and America, printing machines by companies such as BOBST are used for direct process printing at around 100 lines with a register accuracy of 0.3 mm, on everything from food containers to large home appliances such as televisions. Direct printing is currently the norm for full-color carboard packaging in the U.S. and Europe. In recent years, Japanese direct corrugated printing presses have become increasingly accurate and it seems a foregone conclusion that Japan will soon catch up with the U.S. and Europe.
Regarding resin plates, it is common in Japan to use 2.84 mm plates for direct process printing.
As for platemaking, in the process of converting data into resin plates it is important to control for various factors such as printing machine, ink, design, etc.
Cardboard Direct Semi-process Printing
Many Japanese printers use 3 color presses which don’t allow for the same depth of color as 4 color (CMYK) process printing. Therefore, semi-process printing can be used to express vibrant colors using a limited palette of the 3 colors (such as the 3 primary colors). By using 3 colors of ink, you can create eye-catching displays with a different feel to conventional prints. The below photo shows an example using navy blue, yellow, and peony to create a unique combination.
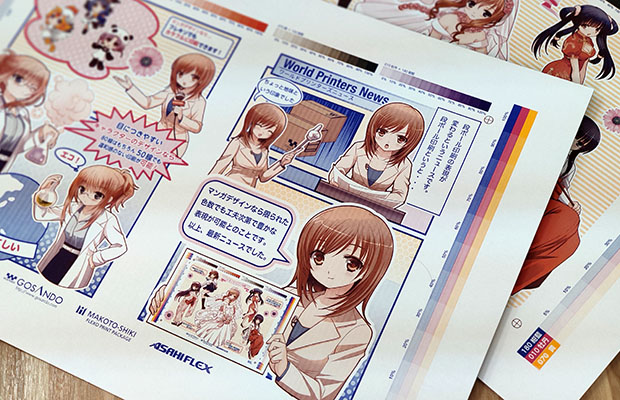
apanese manga were not originally illustrated in full color. However, these line drawings are often an item that is expressed in 3 color flexo printing. Our company has a wealth of experience designing flexo plates to achieve this full color transition. In Japan these manga items as well as local mascot characters are incredibly important to convey the spirit and local specialties of the country.
In Japan, cardboard is usually very plain and practical compared to other countries around the world. It has traditionally been seen purely as a logistical item however the reality is that a box will be viewed by many eyes on its way to the end consumer, and a visually appealing package is a great way to promote your product or brand.
Making cardboard colorful, not only increases the perceived value of your products, but also provides an opportunity to naturally raise your brand’s image among consumers and distributers.